What is Spacecraft Multilayer Insulation?
Managing extreme temperatures is a critical aspect of successful missions. Spacecraft multilayer insulation, MLI, is engineered specifically to address these challenges by providing essential thermal protection. This sophisticated technology uses multiple layers of reflective materials to control the internal thermal environment effectively, safeguarding sensitive equipment and maintaining structural integrity. Quest Thermal Group, a pioneer in this field, continues to lead advancements in spacecraft multilayer insulation, enhancing the performance and reliability of missions through innovative insulation solutions.
Overview of Spacecraft Multilayer Insulation
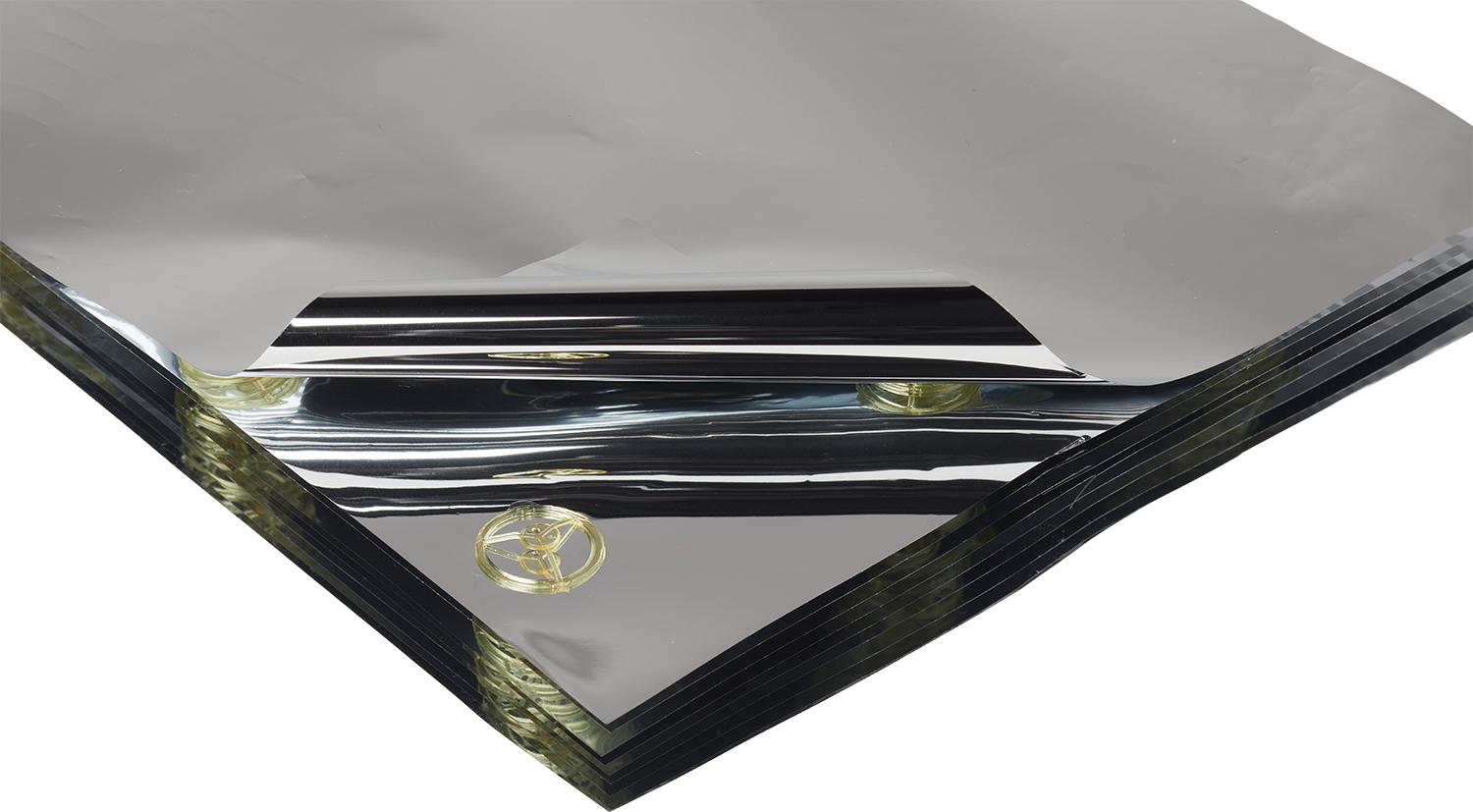
Spacecraft multilayer insulation comprises several layers, including reflective films and materials. These reflective films are typically made from aluminized materials such as polyimide or polyester, selected for their robust reflective properties and ability to withstand severe conditions. Spacer materials, in the past consisting of fabrics like polyester netting or glass fiber mats, kept the reflective layers separated, but allowed conductive heat transfer between layers, degrading thermal performance. Quest’s advanced Integrated MLI (IMLI) uses low thermally conductive discrete spacers to separate radiant barriers, reduce heat conducted between layers, and support various loads.
How It Functions
The core function of spacecraft multilayer insulation is to reduce radiant and conductive heat transfer between the spacecraft, often cryogenic propellant tanks in the vehicle, and the harsh environment. It achieves this through its multiple reflective surfaces that reflect thermal radiation away from the craft and low thermal conductance separators or spacers between the layers. In the vacuum of space, where convection is absent, thermal transfer occurs via radiation and conduction. Multilayer insulation with radiant barrier layers and spacers effectively reduce radiated and conducted heat transfer, helping maintain the internal temperature of cryogenic propellant tanks, reducing critical boil off losses.
Benefits
Integrating advanced spacecraft multilayer insulation into design offers numerous advantages:
- Reduced boil-off losses of cryogens: cryogens such as liquid hydrogen, liquid oxygen and liquid methane are used as propellants or to maintain very low temperatures for sensitive detectors.
- Low temperature sensors: Some sensors and detectors require low temperatures to operate effectively. Insulation helps maintain these conditions, ensuring optimal functionality.
- Energy Efficiency: MLI can reduce the reliance on onboard heating or cooling systems, which are often significant energy consumers. This efficiency is crucial, especially for long-duration missions where energy conservation is paramount.
- Enhanced Structural Integrity: Repeated thermal cycling—exposure to extreme heat followed by extreme cold—can weaken structural materials over time. Spacecraft multilayer insulation stabilizes these temperature variations, thus protecting the structural integrity.
Quest Thermal Group’s Innovations in Spacecraft Multilayer Insulation
Quest Thermal Group’s contributions to MLI technology are substantial. We focus on enhancing the thermal performance and durability of the systems while minimizing their weight. This is particularly important in aerospace applications where every gram counts. Our innovative approaches include the use or our proprietary Discrete Spacer Technology (R), novel vapor cooling methods, load bearing structural MLI, and lightweight spacer-supported vacuum shells.
Practical Applications of Spacecraft Multilayer Insulation in Space Missions
The versatility of spacecraft multilayer insulation makes it essential for a wide range of missions:
- Satellites: Whether for communication, Earth observation, or scientific research, satellites rely heavily on multilayer insulation to protect their sensitive electronic components from the thermal extremes.
- Manned Spacecraft: Human missions, such as those to the International Space Station or planned missions to the Moon and Mars, depend critically on effective thermal management systems. IMLI ensures that the habitat modules remain within habitable temperature ranges, and enables near Zero Boil Off of cryopropellants.
- Interplanetary Probes: As these probes travel through space to different celestial bodies, they encounter varying thermal environments that can drastically affect instrument performance and data integrity. Spacecraft multilayer insulation is pivotal in ensuring these instruments remain functional.
Extending the Frontier of Space Exploration with Advanced Insulation
As exploration ventures further and missions become more complex, the role of spacecraft multilayer insulation becomes increasingly significant. Quest Thermal Group’s ongoing research and development in this area is not only enhancing the capabilities of current missions but are also laying the groundwork for future exploration efforts. By improving the thermal management technologies used in spacecraft, Quest is helping to enable longer, more ambitious missions, such as manned Mars missions, where robust and efficient thermal control will be critical.
Conclusion
Spacecraft multilayer insulation is a fundamental technology in aerospace engineering, providing crucial thermal protection that ensures the success and safety of missions. Through innovative design and material advancements, we are at the forefront of developing new technology that helps solve critical cryogenic fluid management challenges for long duration space exploration missions.
As we continue to push the boundaries of human knowledge and capability, the evolution of multilayer insulation for spacecraft will remain a cornerstone in our quest to explore the unknown, safeguarding both technological investments and human lives against the extreme challenges of the space environment.